Manual handling injuries in the workplace can have serious consequences for both employees and employers. Every year, countless workers suffer from injuries caused by improper lifting, carrying, or moving of objects. These types of injuries at work not only result in pain and suffering for the individuals involved but also lead to lost productivity, increased healthcare costs, and potential legal liabilities for companies. In this article, we will explore the five main injuries that can arise from manual handling and discuss the importance of implementing safe practices in the workplace.
The Five Main Injuries from Manual Handling
Back Strains and Sprains
Back strains and sprains are among the most common injuries resulting from manual handling tasks. These injuries occur when the muscles, ligaments, or tendons in the back are stretched or torn due to excessive force or improper lifting techniques. Employees who regularly engage in tasks such as lifting heavy boxes, bending, or twisting are particularly susceptible to these injuries. Back strains and sprains can cause severe pain, limited mobility, and in some cases, long-term disability.
Shoulder Injuries
Shoulder injuries are another common consequence of improper manual handling. When workers repeatedly lift or carry heavy objects using their shoulders, the rotator cuff muscles can become strained or torn. These injuries not only result in pain and discomfort but can also limit an individual’s ability to perform everyday tasks. For instance, a warehouse worker who sustains a shoulder injury may struggle to reach items on high shelves or perform overhead movements.
Hernias
Hernias are a type of injury that occurs when an organ or tissue protrudes through the wall of the cavity in which it is normally contained. In the context of manual handling, hernias often develop due to the excessive strain placed on the abdominal muscles during lifting or carrying heavy objects. Workers who regularly engage in tasks that involve lifting heavy loads without proper support or assistance are at risk of developing hernias. These injuries typically require surgical intervention and can result in significant downtime for the affected individuals.
Slips, Trips, and Falls
While not directly related to lifting or carrying objects, slips, trips, and falls are frequent occurrences in workplaces where manual handling is involved. Employees may slip on wet or uneven surfaces, trip over objects left in walkways, or fall from heights while attempting to move heavy items. These accidents can lead to various injuries, including broken bones, sprains, concussions, and even more severe consequences. Employers must maintain a safe and clutter-free work environment to prevent such incidents.
Musculoskeletal Disorders
Musculoskeletal disorders (MSDs) encompass a wide range of injuries and conditions affecting the muscles, bones, tendons, ligaments, and other support structures of the body. These disorders can arise from prolonged and repetitive manual handling activities, such as constant lifting or carrying of heavy loads. Common MSDs include tendinitis, carpal tunnel syndrome, and bursitis. Such injuries can be debilitating and significantly impact an employee’s ability to perform their job effectively.
The Importance of Safe Manual Handling Practices
Preventing manual handling injuries requires a proactive approach from both employers and employees. Here are some key measures that can be taken to minimize the risk of such injuries:
Training and Education
Employers should provide comprehensive training to their staff on safe manual handling techniques. This training should cover proper lifting and carrying techniques, the use of mechanical aids when available, and the importance of maintaining good posture. Regular refresher courses can reinforce these practices and help employees stay updated on the latest safety guidelines.
Risk Assessment
Conducting regular risk assessments is crucial for identifying potential hazards in the workplace. By analysing the tasks that involve manual handling, employers can pinpoint areas that pose a higher risk of injury and take appropriate measures to mitigate those risks. This may involve implementing changes in work processes, providing additional equipment or support, and ensuring that the environment is well-maintained and free from hazards.
Making an Injury at Work Claim
When an employee sustains a manual handling injury in the workplace, they may be entitled to make a compensation claim. It is crucial to understand the process involved in filing such a claim to ensure that the injured party receives the support they need. Here are the key steps involved in making an injury at work claim:
Report the Injury
The injured employee should immediately report the incident to their supervisor or manager. Prompt reporting ensures that the details of the incident are documented accurately and helps establish a clear timeline of events.
Seek Medical Attention
Seeking medical attention is crucial for assessing the extent of the injury and receiving appropriate treatment. The injured party should visit a healthcare professional or the company’s designated medical provider as soon as possible. The medical records will serve as valuable evidence when filing the claim.
Consult with National Claims
Seeking legal guidance from National Claims, an experienced injury at work claims specialist. We can guide you through the claims process, help gather evidence, and advocate for your rights. We will assess the viability of the claim and provide expert advice on the potential compensation that can be sought.
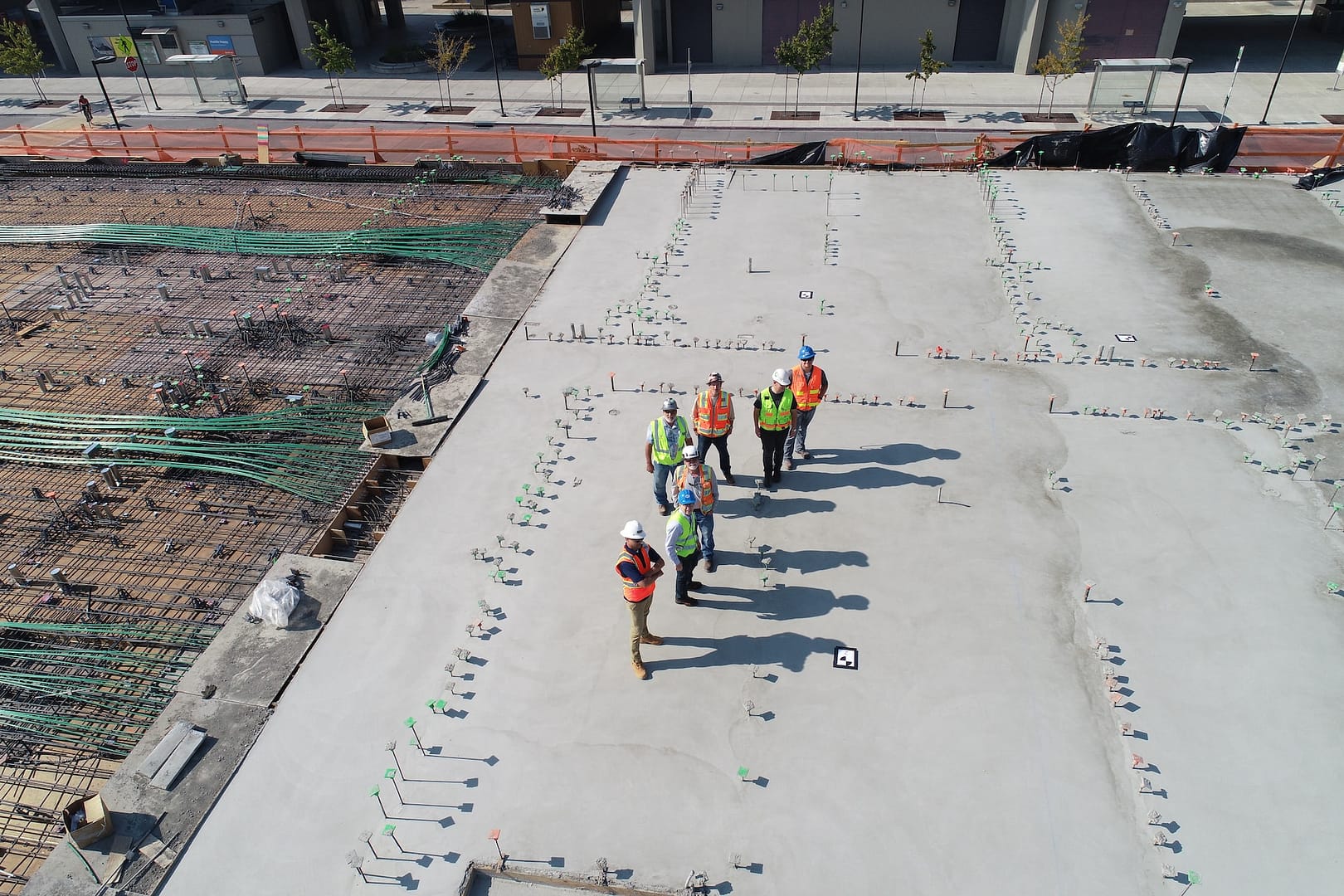
Conclusion
Manual handling injuries in the workplace can have far-reaching consequences, affecting both individuals and organizations. By understanding the common injuries associated with manual handling and implementing safe practices, employers can minimize the risks and promote a safer work environment. Additionally, providing training, conducting risk assessments, and prioritizing ergonomics can further reduce the incidence of injuries.
In the unfortunate event of a manual handling injury, it is important for you to be aware of their rights and the process of making an injury at work claim. Seeking timely medical attention, gathering evidence, and consulting with us at National Claims will help ensure that you receive the support and compensation you deserve.
Contact us today to start your work accident compensation claim and get further help from our experienced team of claims specialists.
Click below to see why we are one of the most trusted claims management companies in the UK.