When it comes to the safety of employees in industrial settings, “Machinery Lockout Procedures” play a pivotal role in preventing accidents and ensuring a secure work environment. In this article, we will delve into the world of lockout procedures, understand what they entail, and explore how they effectively safeguard the lives and well-being of those working with heavy machinery. Lockout procedures are not merely a set of guidelines; they are a lifeline for workers, and in the UK, they are taken very seriously to ensure employee safety.
What is a Lockout Procedure?
Before we dive into the details of how lockout procedures ensure employee safety, it’s essential to comprehend what a lockout procedure actually is. In its simplest form, a lockout procedure is a set of practices and protocols that are put in place to isolate machinery or equipment from its energy sources, making it inoperative and safe to work on.
In an industrial setting, machinery is often powered by various energy sources, including electricity, hydraulics, pneumatic systems, and even gravity. These energy sources can pose serious risks to employees if not properly controlled during maintenance, repair, or servicing activities. A lockout procedure typically involves the following key steps:
Identification: Identifying the machinery or equipment that needs to be locked out. This step includes marking, tagging, or labelling the equipment to be serviced.
Notification: Informing all employees who might be affected by the lockout. This ensures that no one inadvertently starts or operates the machinery during servicing.
Isolation: Physically disconnecting the machinery from its energy source by turning off switches, valves, or other control mechanisms.
Locking: Using locks to secure the energy isolation devices. This step prevents the equipment from being accidentally turned on while work is being carried out.
Verification: Confirming that the energy isolation is effective by testing the equipment to ensure it cannot be started.
Work on Machinery: Once the machinery is locked out and verified as safe, employees can proceed with maintenance, repair, or servicing.
Removal of Locks: After the work is complete, the locks and tags are removed, and the equipment is returned to normal operation.
Lockout procedures are highly detailed and may vary depending on the machinery or equipment involved. They are tailored to specific machines and energy sources, and they must be strictly followed to ensure employee safety.
How Do Lockout Procedures Keep You Safe at Work?
Lockout procedures are not just a series of steps written on paper; they are the embodiment of a culture of safety in industrial workplaces. These procedures are the bridge between potentially dangerous machinery and the well-being of the workforce. Let’s take a closer look at how lockout procedures ensure employee safety:
Preventing Accidental Start-ups
Imagine you are an electrician tasked with repairing a massive conveyor belt in a factory. Without a lockout procedure in place, the conveyor could potentially start moving while you’re working on it, leading to severe injury or even a fatality. Lockout procedures prevent these accidental start-ups by physically disconnecting the equipment from its power source and ensuring it remains inoperative.
Clear Communication
One of the cornerstones of lockout procedures is effective communication. When a machine or piece of equipment is locked out, it is typically tagged or labeled to make it clear to all employees that work is in progress. This way, anyone passing by or potentially interacting with the machinery knows to stay clear and not to attempt to operate it. Effective communication in lockout procedures is a crucial element in ensuring the safety of all employees.
Personal Accountability
Lockout procedures require employees to use personal locks and keys to secure the energy isolation devices. This means that each worker is responsible for their own safety. By placing this level of personal accountability on employees, it encourages them to take the procedures seriously and ensures that they are actively involved in their safety.
Verification of Safety
Before any work can begin on a locked-out machine, there is a critical step that ensures the machinery is, in fact, safe to work on. This verification step involves testing the machine to confirm that it cannot be started. This extra layer of safety ensures that the equipment is truly inoperative and that employees can safely proceed with their tasks.
Preventing Unplanned Energy Release
Unplanned energy release is a significant hazard in industrial settings. When machinery is not properly locked out, stored energy in the system can suddenly release, leading to accidents and injuries. Lockout procedures minimise this risk by systematically isolating and de-energising equipment.
Legal Compliance
Lockout procedures are not just a best practice; they are often a legal requirement. In the UK, the Health and Safety at Work Act and other regulations mandate the implementation of safety procedures, including lockout procedures, to protect employees. Failing to comply with these regulations can result in fines and legal consequences.
Safety Training
Proper lockout procedures require training and education. In the UK, employers are obligated to provide training to employees on lockout procedures, ensuring that they understand the process and can follow it effectively. This training not only enhances safety but also empowers workers to take responsibility for their own well-being.
A Culture of Safety
Lockout procedures are a cornerstone of creating a culture of safety in the workplace. They send a clear message to all employees that their safety is a top priority. When workers see that their employer takes safety seriously, they are more likely to be vigilant and cautious when working around machinery.
Prevention of Catastrophic Accidents
It’s essential to acknowledge that lockout procedures are not merely for minor safety issues. They are crucial in preventing catastrophic accidents. These procedures can mean the difference between a minor incident and a life-altering or fatal accident. They serve as a safety net that protects employees from the potential hazards of working with heavy machinery.
Making an Accident at Work Claim with National Claims
At National Claims, we understand the importance of employee safety and the role that lockout procedures play in preventing workplace accidents. However, we also recognise that accidents can still happen, even when the strictest safety measures are in place. In such unfortunate situations, employees may need to make an accident at work claim to seek compensation for their injuries.
National Claims is here to guide and support you through the process of making an accident at work claim. Our experienced team of legal experts specialises in workplace injury cases and understands the intricacies of the legal system in the UK. We are committed to helping you receive the compensation you deserve if you’ve been injured in a workplace accident due to the negligence of others.
The process of making an accident at work claim involves several key steps:
Initial Consultation: The first step is to contact National Claims for an initial consultation. During this consultation, we will gather information about your accident, the extent of your injuries, and the circumstances surrounding the incident.
Assessment of Eligibility: Our legal experts will assess the eligibility of your claim. We will determine if there is sufficient evidence to establish that your injuries were a result of negligence or unsafe workplace conditions.
Collecting Evidence: To build a strong case, we will work with you to collect all necessary evidence, including medical records, witness statements, and any relevant documentation regarding the accident and your injuries.
Negotiation with the Employer: In many cases, we will attempt to negotiate a settlement with your employer or their insurance company to compensate you for your injuries. Our goal is to secure a fair and just settlement that covers your medical expenses, lost wages, and any additional damages.
Claim Resolution: Once your claim is successfully resolved, you will receive the compensation you are entitled to. This can help cover medical bills, rehabilitation costs, lost income, and other related expenses.
At National Claims, we understand the emotional and financial toll that workplace injuries can have on your life. Our dedicated team is here to provide you with the legal support and guidance you need during this challenging time. We are committed to helping you achieve a fair outcome and receive the compensation you deserve.
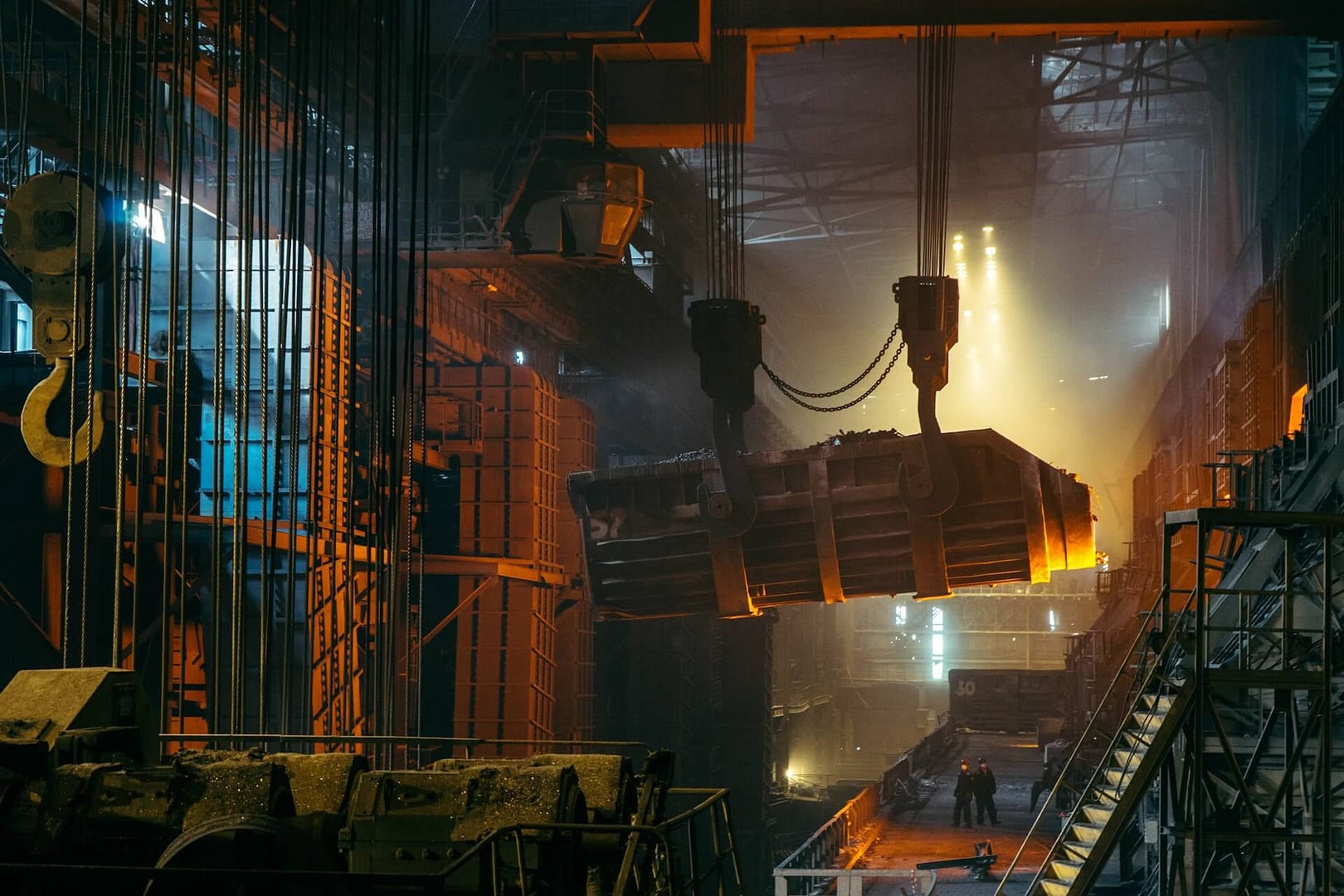
Conclusion
In the world of industrial work, safety is paramount. Lockout procedures are a vital component in ensuring employee safety in the UK and across the globe. These procedures are not just guidelines on paper; they are a way of life in industries where machinery and heavy equipment pose inherent risks.
Lockout procedures prevent accidental start-ups, promote clear communication, instil personal accountability, verify safety, and prevent unplanned energy releases. They also ensure compliance with legal regulations, provide necessary safety training, cultivate a culture of safety, and, most importantly, prevent catastrophic accidents.
For employees in the UK and beyond, following lockout procedures isn’t just a matter of compliance; it’s a matter of life and death. By implementing and adhering to these procedures, companies can protect their most valuable assets—their employees—and create a safer, more productive work environment. In the end, it’s not just about locking down machinery; it’s about locking in the safety and well-being of those who keep industries running.
If, despite all precautions, you find yourself injured due to a workplace accident, National Claims is here to support you in making an accident at work claim. We are dedicated to ensuring that employees who have suffered injuries due to workplace negligence receive the compensation they deserve. Your safety and well-being are our top priorities, and we are here to assist you in navigating the legal process to achieve a fair and just resolution for your injuries.
Contact us today to get started on your claim and speak to one our claims specialists.
Click below to see why we are one of the most trusted claims management companies in the UK.
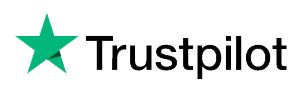
We’re proud of our excellent customer reviews
We thrive on delivering exceptional service and ensuring our clients’ satisfaction. Don’t just take our word for it. Check out some of our independent reviews to see what our clients have to say.
Excellent
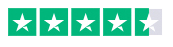
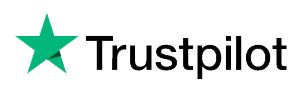
This firm is excellent, they sorted out my car pay out and injury claim very fast, they always communicate with you all the time.

My accident case was dealt with confidence and with great result of the outcome, especially James kept me informed all the time.

I was very impressed at the way my inquiry was treated. I was listened to attentively and everything I needed to know was explained to me.
